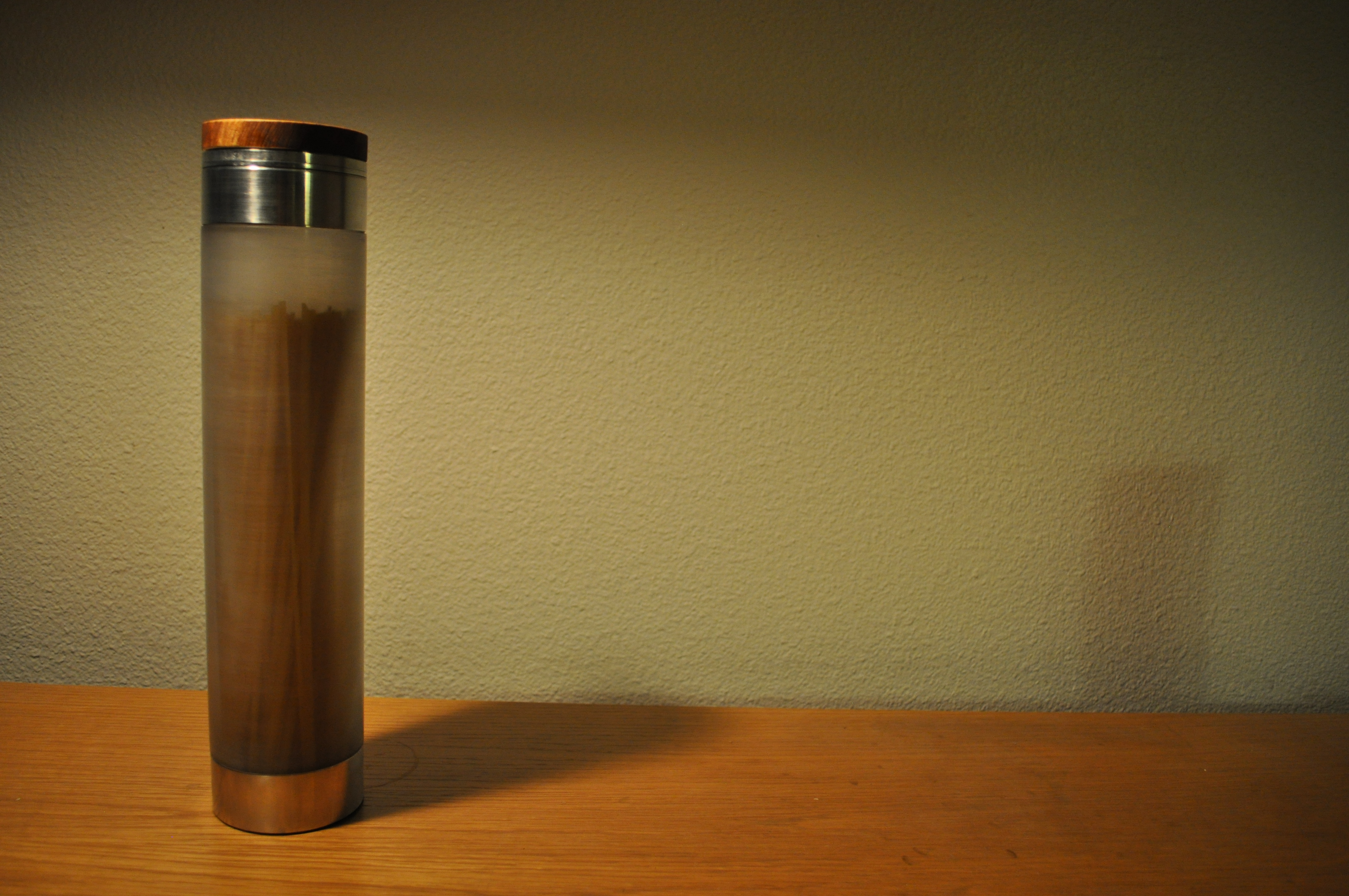
As an Embrace alumni, I have a deep appreciation for design, design thinking, and the power of form in helping realize a product’s value. Upon arriving at Stanford, my buddy Rajan Patel shared with me how transformative Dave Beach, the Product Realization Lab, and specifically the “Introduction to Machining” course (ME203) had been for him. I was hooked and knew I had to take the course the second I got to campus.
ME203 is an intensive 10-week course: in the first two weeks, all students are taught how to mill, lathe, use a foundry (sandcasting), and weld … ! We use that to build a magnifying lens and a plaque of the Stanford crest, and have to finish them professionally. Once that’s been completed, all students undertake a project of their choosing over the next ~6 weeks. I decided to build a pasta holder for my girlfriend, Andrea.
Background
I came up with this product idea before Andrea had moved back to the United States. We met in Bangalore, and I came back to start school 7 months before she got to the Bay Area. Due to terrible timing, I ended up choosing classes that would take 70-80 hours a week just as she arrived. I thought that if I could make something *for* her about her *favorite food*, I might be able to get away with being so absent. :)
A prompt for the product is to determine a “critical part.” This is the design attribute in the product that everything is built around and must be successful. I decided that I would have two - since Andrea was traveling so much, I wanted to index on durability and freshness. I chose polycarbonate and aluminum as materials that would support that.
Machining on a lathe
Every part I built was done on a lathe. I was doing some interesting things - for example, working on both ends of a 12’-long 1/8”-thick piece of polycarbonate - that required developing some savvy and using niche parts like a center pivot and creating extra pieces as reinforcement so that the part wouldn’t deform the plastic.
Prototyping, CAD, and BOMs
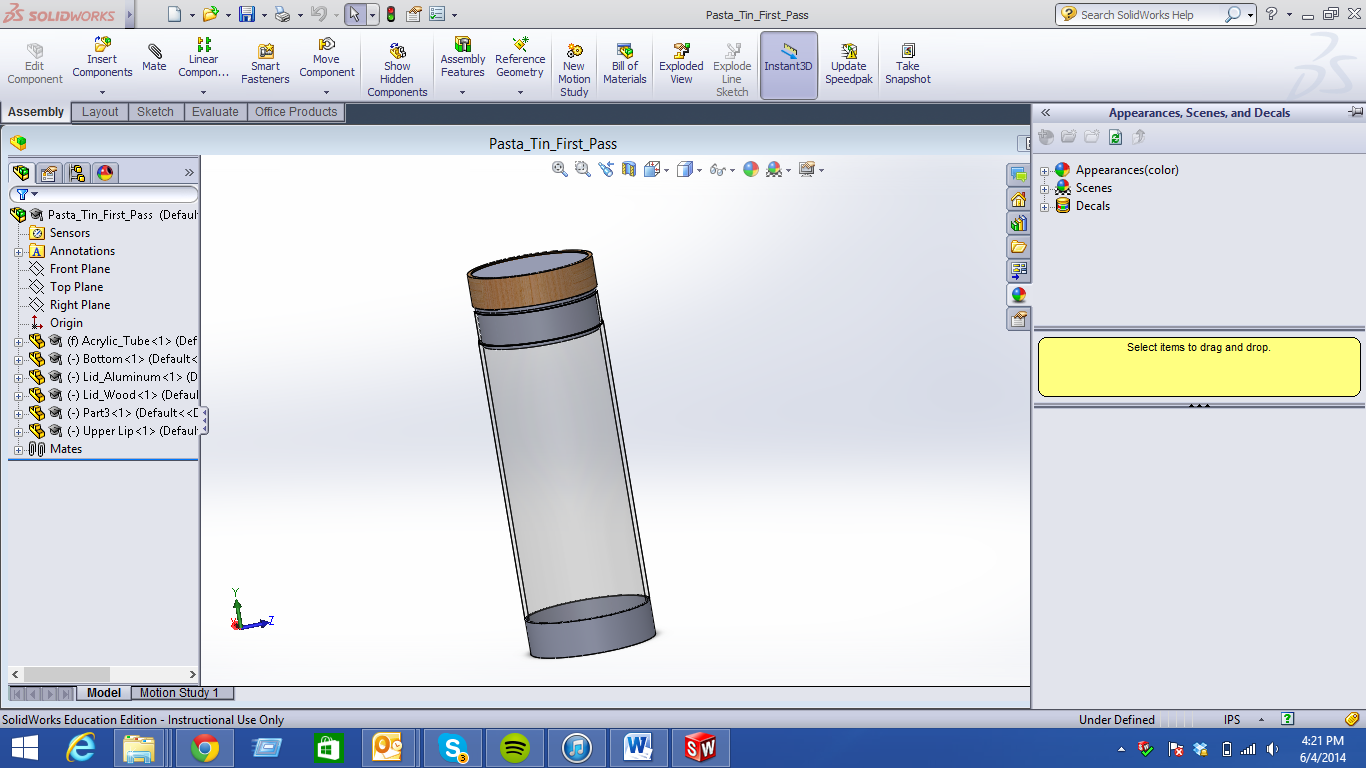
Personally, my exploration into prototyping didn’t extend far beyond looking at different threading types. This was a mistake as, had I prototyped, there would have been several things that I did differently in my final product. For example - my cap is solid aluminum, and it gives the product a top-heavy feel. I wanted it to have a “light, California feel.” This is why I used solid, natural materials and gave them a clean finish instead of doing anything extra. With some prototyping, I would have cut some more material out of my lid to give it the balance I was looking for.
An endless series of broken things
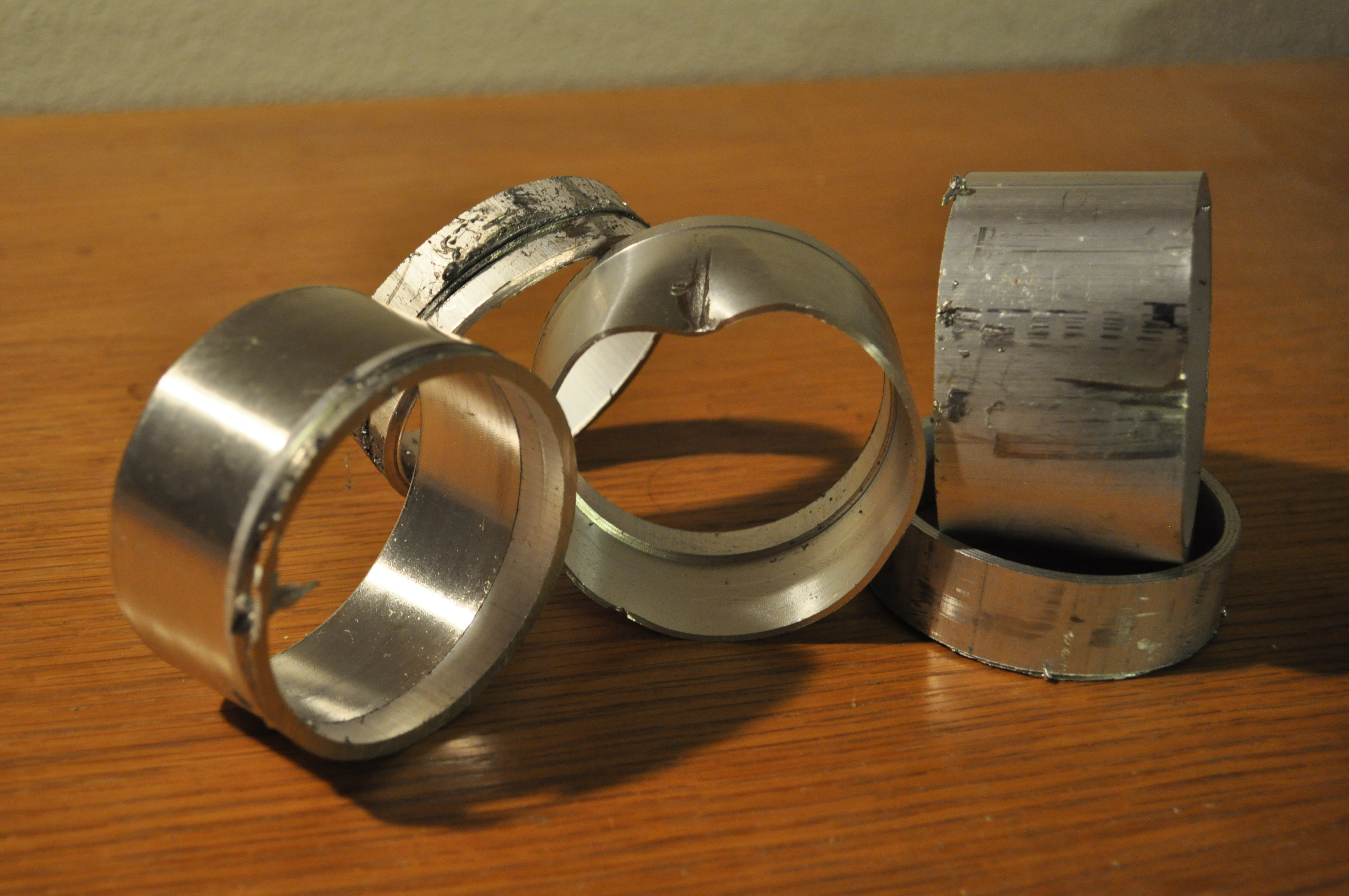
My design was a relatively simple concept, and I expected that I would be able to build it quickly and focus on design extensions – such as using a laser cutter or adding steel plating fixtures. Then, my first 4 aluminum ribbons (.050” thick) broke – and I lost 16 hours of lab time. Two of them broke when parting, and in one instance, the parting tool broke!
- The parting tool must be perpendicular to the surface, it should be set off of the
- Each time the part is removed and placed again on the lathe, a new center point is established – never finish working when you are .030” from finishing your cut.
- If you want it done right – for the circles to be perfectly concentric – don’t take the product off the late.
- If you want it to be okay, make sure to use the dial calipers to ensure circularity.
I now can make this part in 2 hours – but it actually took me 18 hours to get there. And if I had made the part perfectly the first time, I probably wouldn’t have learned any of this (because I wouldn’t have realized what worked for me!).
The final product!
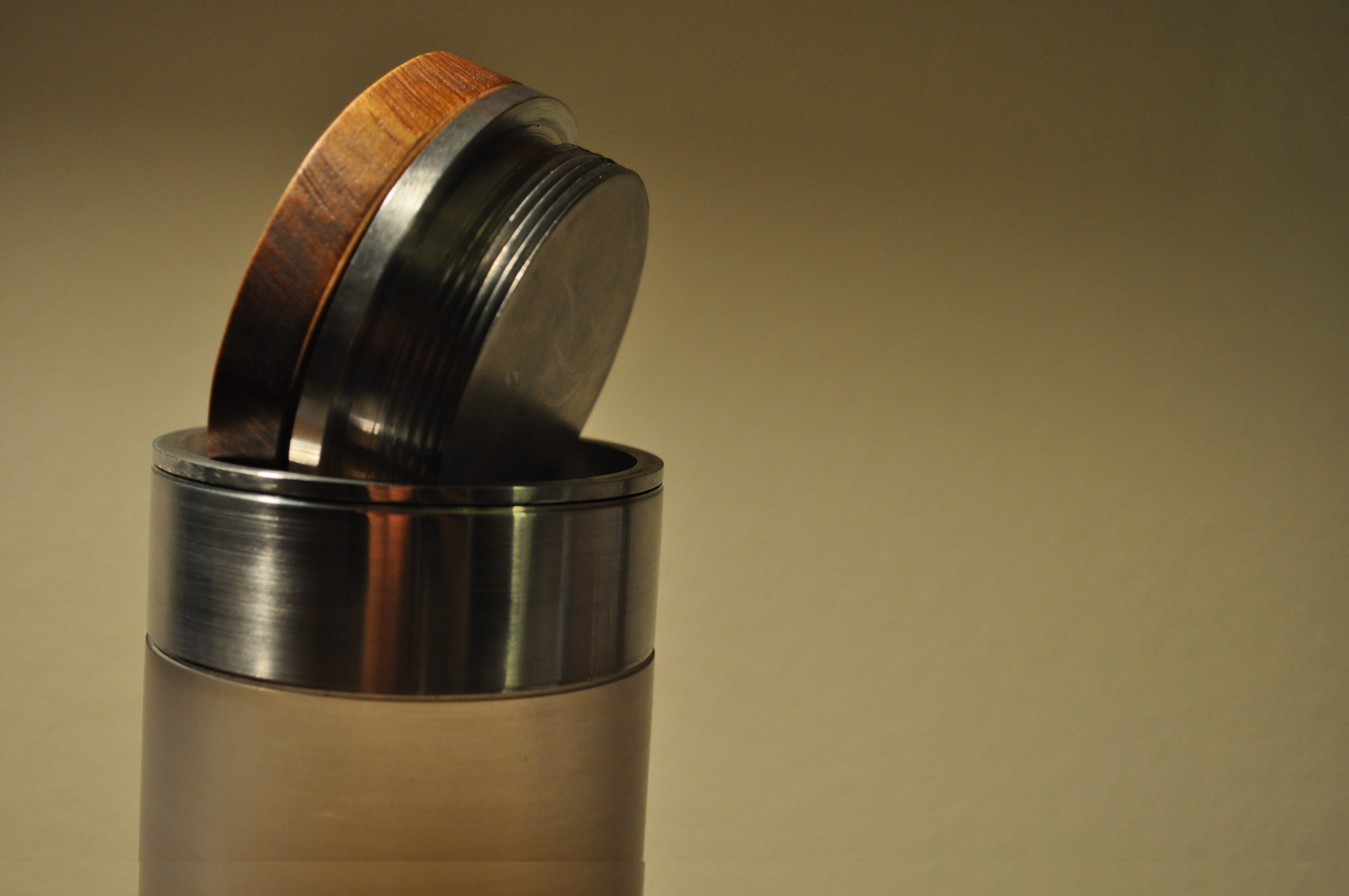
Once I had all of my pieces finished, I needed to assemble them. I had designed a .0050” ribbon of aluminum to fit over a polycarbonate ridge. They had a tolerance overlap of .0005” so that friction would hold them together. I pushed them together on an arbor press and breathed a HUGE sigh of relief when it slipped on without breaking. I had spent so much time, and broken so many parts, that I think I might have cried if this didn’t work.
I also added a “reveal” between where the aluminum and the polycarb met on the outside of the product. This was done so that when a user runs their finger along the interface, it’s impossible to tell if there might be some inconsistency in the shapes of the two pieces. It fools your brain into thinking it is a perfectly smooth join, and is used commonly when manufacturing PCs & Macs.
Lessons learned
ME203 was a great experience for me, and a jumping point for being able to move into increasingly more technical projects. Here were a few of my big lessons:
- I love products. Growing up, my family was actually known for its design abilities. My grandfather was a pilot; my dad and his brothers raced sprint cars on open-wheel dirt tracks. They were known for getting more out of cheaper products, because they built their own cars. I grew up on the smell of cut metal and grease. My brother worked in the pit crew for an IndyCar. In a small way, being a part of this class has brought me closer to my family. It’s been fun getting to share with them the experience of the class, and the joys and frustrations of working with the materials to realize a concept.
- Prototyping only works if you know what you’re testing. In building the product, I made many decisions on the fly – I was balancing cost, available products, and anticipated aesthetics. Initially, I thought I didn’t need to prototype because I had one joining function (threading) and I knew what the product would look like aesthetically. At the end, I realized that I could have explored and experimented with all of these factors had I known to look for them in my prototypes.
- “You have to ‘go’ to know.” – Tony Scott. Tony is an older GSB alum who has credited his career to his willingness to use new experiences as a learning process. I am glad to have taken this course as I wouldn’t have had the ability to articulate these learnings any other way.
-
Production & design are both art and science. Before taking this course, I thought of manufacturing as an exact science. One knows what their technical specifications are, and then they press a button and many parts are produced in cookie cutter fashion. I’m being slightly simplistic, but this is a close approximation.
That’s not the case. Parts wear; people get tired. Cuts slip. Press fits change between materials. Many joining parts are guided by “what feels right.” Designs change as one considers cost and “what’s available.” Even though the process involves a machine, it is much less mechanical than one might think from the outside.
It’s a bit funny/silly, but I also got to make a summary video of the project in lieu of being present for the final. It says much of the things covered in this post, and can be found here.
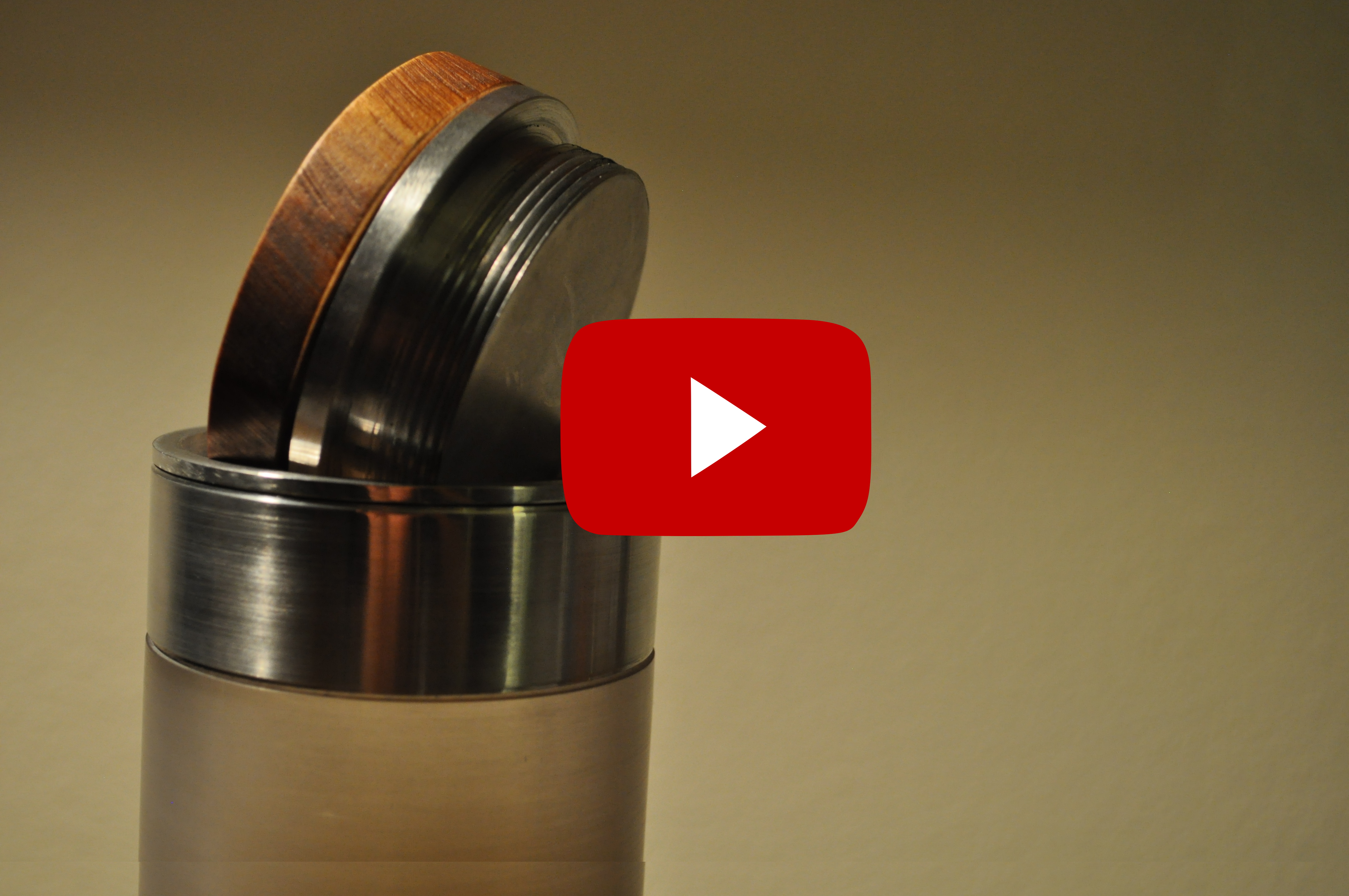